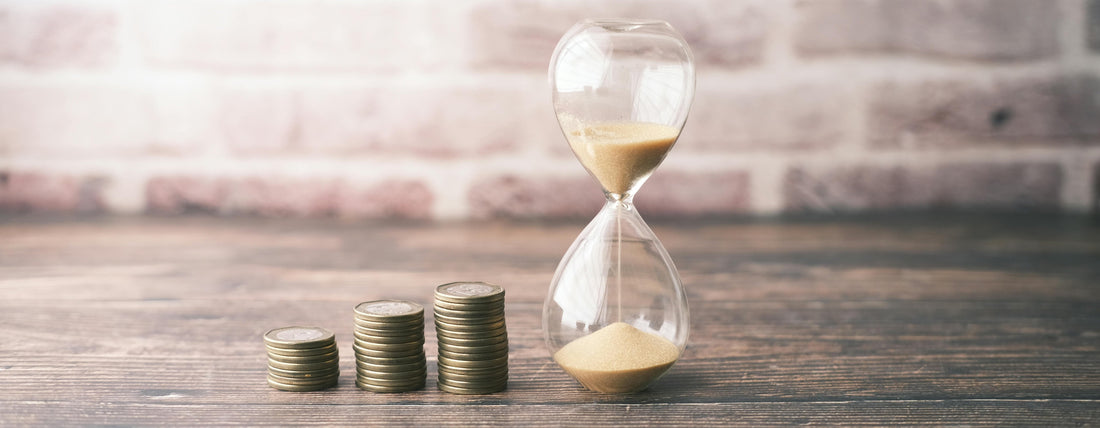
5 Ways Industrial Supplies Can Save You Time and Money
Share
In the fast-paced world of warehouses and industrial operations, efficiency and cost-effectiveness are critical. The right industrial supplies can do more than just simplify tasks—they can significantly reduce expenses and save valuable time. Here's how:
1. Improved Efficiency with the Right Tools
Investing in specialized tools increases productivity by speeding up operations. Here are some examples:
Pallet Jacks: A high-quality pallet jack can move heavy loads quickly and easily, reducing labor time by up to 30%.
Example: If employees save 2 hours daily by using an efficient pallet jack, at $20/hour wage, that’s $800/month saved.
Industrial Shelving: Well-organized storage reduces time spent looking for items. Workers can retrieve products 40% faster with proper shelving.
Example: If retrieval time drops by 30 minutes/day for a team of 5, you save $1,500/month in labor costs.
2. Reduced Maintenance Costs
Durable industrial supplies last longer, requiring fewer repairs or replacements.
Example: A low-quality pallet jack costing $300 may need replacement every 2 years. A high-quality one costing $700 could last 5 years or more. Over 5 years, you save $800 in replacement costs.
3. Enhanced Worker Safety
Investing in safety gear minimizes workplace accidents, which can be expensive.
Example: OSHA estimates the average cost of a workplace injury is $42,000. By using proper safety supplies like helmets, gloves, and anti-slip mats, businesses reduce accidents by up to 70%, potentially saving tens of thousands of dollars annually.
4. Lower Energy and Operating Costs
Energy-efficient tools and equipment reduce utility bills.
Example: Replacing traditional warehouse lighting with LED lights:
Monthly electricity costs with halogen: $500.
Monthly costs with LED: $200.
Savings: $300/month or $3,600/year.
Upgrading to energy-efficient pallet trucks could reduce fuel or electricity costs by 20%, saving $2,000/year on a fleet.
5. Scalability and Future-Proofing
Investing in modular, high-quality supplies prepares your business for growth without frequent upgrades.
Example: A modular shelving system that costs $5,000 can expand with your inventory needs, eliminating the need for a $10,000 warehouse redesign in the future.
Conclusion
By investing in the right industrial supplies, businesses can save thousands annually while improving efficiency and safety. This not only enhances daily operations but also strengthens your bottom line over time.
Would you like to feature any of your products as examples for these savings? I can help tailor this further!